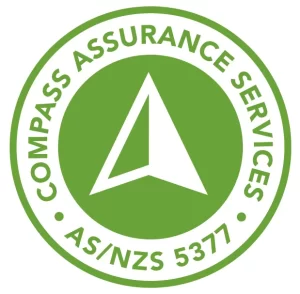
AS/NZS 5377 Checklist
AS/NZS 5377 E-Waste
Section 1 – Scope, Objective, Application & General Requirements for Head Office Activities
Mandatory Documents
Risk Assessment Process and schedule to review risk assessments (as per 1.6.3)
List of products and waste materials that you are capable of handling in a safe and environmentally compliant (as per 1.6.3)
An emergency response plan Including clean-up/remediation methodologies and validation (as per 4.1)
Training materials and information for, but not limited to, risks of substances in Appendix B (as per 1.6.6)
Section 5: Treatment Only:
- Documentation of the point of final disposal including Waste Storage Licenses and Waste Transport Licenses from all jurisdictions where required, such as permitting/licensing of transport vehicles (as per 5.3)
- Documented evidence of import and/or export permits (if applicable) (as per 5.3)
Key Records
Competency documentation for tasks with environmental and safety impact (1.6.5)
Traceability records for equipment, parts, and waste (1.7)
Records of end-of-life components for re-use (3.3)
Documentation for classified waste transportation (4.4)
Mass balance records for processing facilities (5.3)
Need a Quick Quote?
Request an obligation free quote today, tailored specifically to your business’ certification needs and industry.
Get Your Free ISO Checklist
Training Sessions
Contact Us
General Requirements
Have you integrated end-of-life electrical and electronic equipment management into existing environmental or similar systems?
Do you have processes to update and communicate legal and other obligations to stakeholders?
Have you Identified Legal and Other requirements including:
- Environmental and Health and Safety Legislation
- Site Licensing and licenses for the handling, storage, transport and treatment of end-of-life electrical and electronic equipment
- Export Licenses and regulations
- International treaty obligations
Organisational Requirements
Licensing
Are you facilities and operators authorized in accordance with the relevant legal and other requirements pertaining to the location in which the facility is situated
Emergency Response
Is there an emergency response plan in place for on-site and off-site incidents, including:
- Pollution releases,
- Spills
- Storms
- Floods
- Earthquakes
- Medical incidents
This includes notification provisions, recovery timelines, clean-up methodology, training, and documentation?
Are drills conducted at appropriate times?
Risk Assessment Management
Do you have documented risk assessment processes to identify and control potential environmental and safety hazards associated with the operator?
Do you maintain a list of safe products and waste materials?
Training Material
Are training materials easily accessible and cover all relevant risks, including substances of concern?
Have you considered using technical guidance documents, risk assessments/safety statements, information charts/tables, photos/examples of components, and safety data sheets for hazardous substances as part of your training materials?
Training
Have you trained and kept records of competence for person(s) performing tasks that have the potential to cause an environmental or safety impact(s)?
Records Management
Do you keep record to allow the traceability of equipment, assemblies, parts, commodities and waste? Do these include:
- Manifests, bills of loading, chain of custody documents, transport records?
- Any other record keeping requirement outlined in this Standard
Are these records accessible, identified, legible and maintained for at least five years?
Data Security
Have you considered the need to prominently display advice at your collection locations for the process for removing private or confidential data?
Have you considered the need to have information available to make the disposer aware that file deletion does not mean privacy data has been fully removed?
Disposal to Landfill
Do you dispose of waste at a waste facility that is licensed to accept the waste?
Re-Use & Refurbishment of Equipment
Do you ensure that equipment identified and collected for re-use and refurbishment is collected, stored, transported and treated separately to equipment identified and collected as end-of-life?
Section 2 – Requirements for Collection & Storage
General
Are your facilities authorised according to the relevant legal and other requirements for to the location of your facilities?
Access
Are your public collection areas easily accessible and kept clean and free of hazards?
Signage & Information
Have you provided signage and advertising material to communicate safety warnings, instructions, site access times, equipment details, and disposal of data storage media privacy risks?
Storage & Handling
General
Do you maintain physical integrity of components and prevent hazardous substance release?
Is collected material stored and handled to prevent theft, exposure, and damage, particularly to hazardous substances?
Are breakable parts packaged and loaded carefully?
Do you have necessary tools and receptacles for effective recycling?
Do you undertake on-site disassembly in compliance with Section 5 of the Standard?
Consolidation & Sorting Facilities
Do you ensure that, during the collection, storage and transport of end-of-life equipment, it is not mixed with other types of waste with the same container of receptacle?
Storage Facilities
Is your storage area equipped with impermeable surfaces, weatherproof coverings, and measures to prevent hazardous materials from entering storm water drains?
Do you have a document control procedure that covers document approval, review and updates, revision status, versions, legibility, and required external documents, as well as obsolete documents?
Requirements for Handling & Storing End-of-Life Electrical & Electronic Equipment
Do you have processes for safe storage and handling of:
- Batteries to prevent combustion, explosion or leaking.
- Electrical contacts to prevent short circuits or flows of current.
- Refrigerant systems in receptacles that meet dangerous goods UNEP guidelines.
- CRT displays to prevent implosion or loss of phosphorescent coatings.
- Equipment with hazardous components or materials such as mercury containing lamps and globes, gas discharge lamps, smoke detectors, petroleum fluids, polychlorinated biphenyls (PCBs), and asbestos.
- Wet cell batteries and exposed lithium type batteries, if needed.
Do you also have measures in place to protect against rough handling and damage to these items, to avoid spillages, emissions or release of hazardous substances?
Broken Or Dumped Material
Do you handle, store and dispose of equipment that is broken on-site or dumped in the immediate vicinity in accordance with this Standard?
Section 3 – Recovery for Re-Use From End-of-Life Electrical or Electronic Equipment
Harvesting of Assemblies, Components & Parts
Have you considered the need for:
- Written procedures for the re-use process
- Risk assessment and management systems for re-use
- Removal of distinguishing marks on assemblies, components, and parts
- Record-keeping for incoming and outgoing end-of-life equipment
- Mass balance tracking for received, re-used, and residual waste equipment
- Clear labelling of refurbished and safe-to-use equipment
- Testing of safety and functionality of re-usable equipment
- Compliance with guidelines for handling refrigerants
- Adequate equipment for refrigerant gas processes
- Adherence to relevant electrical safety Standards?
General
Do you repair, refurbish and re-market used whole equipment (outside the scope of this Standard)?
Preparing for Re-use
Do you prepare end-of-life electrical and electronic equipment for re-use by separating and recovering components and parts?
Are re-useable components and parts collected, labelled and stored in weatherproof facilities or receptacles to maintain their functionality and physical integrity?
Management of Residual Waste From Recovery
Do you ensure that non-reusable assemblies, components, and hazardous parts are processed according to Section 5 of this Standard?
Section 4 – Requirements for Transportation
General
Have you considered that some end-of-life electrical and electronic waste parts may be hazardous or regulated?
Do you comply with local transport licensing requirements?
Are you exporting potentially hazardous waste parts in compliance with domestic legislation for transboundary movements?
Objectives of Transporting End-of-Life Electrical & Electronic Equipment
Have you considered minimizing damage and transportation risks when transporting end-of-life electrical and electronic equipment for recovery or recycling purposes?
Do you ensure trained staff use appropriate equipment and handle materials according to Clause 2.4 of this Standard, and maintain documentation for traceable, controlled, hazardous or prescribed industrial waste?
Section 5 – Requirements for Treatment of End-of-Life Electrical & Electronic Equipment
General
Do you monitor hazardous substances, preparations, and components for safe treatment and maximum material recovery?
Traceability
Do you track the material flow from intake to final disposal, including downstream processors, transport, processing, and recovery rates?
Do you maintain source documents verifying all material transfers and re-use sales?
Do you keep documentation on waste storage and transport licenses, safety plans, and import/export permits?
Have you considered implementing a process to evaluate downstream processors for substances of concern based on the Standard?
Recycling & Recovery Record Management
Do you maintain annual records to show that your mass balance is accurate according to Appendix D of the standard?
Does your reporting comply with traceability requirements for Recycling and Recovery Record Management?
Processing & Handling
Do you comply with Table 1 of the Standard when recovering resources from end-of-life electrical and electronic equipment?
Is your handling and storage of end-of-life equipment designed to prevent damage, leakage, and release of hazardous substances into the environment?
Do your processing and separation facilities have dust collection systems, emergency shut-off systems, fire suppression equipment, and other safety/environmental control equipment as required by risk assessment?
Have you removed specific items before processing and managed them in accordance with Table 1 and Appendix B of the Standard?
Have you stored any hazardous materials under cover or in a way that prevents release to the environment?
Do you consider alternative treatment options such as recycling, energy recovery, and incineration instead of landfill as a standard practice for disposing of end-of-life electrical and electronic equipment?
Get your own interactive Checklist
What is AS/NZS 5377 E-Waste Management?
AS/NZS 5377 E-Waste is a management system standard developed by the Australian Government Department of the Environment and the New Zealand Ministry of Environment.
Why do I need AS/NZS 5377 E-Waste Certification?
Since 2011, The National Television and Computer Recycling Scheme (NTCRS) has provided Australian householders and small business with access to industry-funded collection and recycling services for televisions and computers.
What are the benefits of AS/NZS 5377 Certification?
Companies often initially seek certification for external reasons such as getting on preferred supplier’s lists, improving company image and responding to customer demands. The benefits of this are obvious – more work.
How can I get certified?
Getting AS/NZS 5377 certification is a lot easier than you might think, We take you through the three step audit process from your initial enquiry to the final certification decision.
AS/NZS 5377 Certification Throughout Australia
Compass Assurance Services have offices and staff located throughout Australia including Brisbane, Melbourne, Perth, Adelaide, and Sydney.
Want to speak to someone?
Contact Us
Contact us and speak to one of our helpful team about your ISO certification needs. We can offer certification to smaller, niche standards and to other non-accredited (non ISO) standards as well.
Request a Quote
Request an obligation free quote today, tailored specifically to your business’ certification needs and industry.