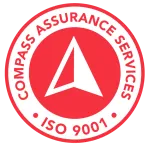
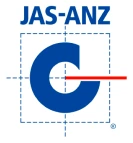
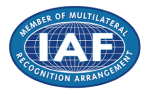
ISO 9001 Certification
ISO 9001 certification is simple. All you need to do is;
- Make your customers happy,
- Eliminate errors, provide a framework that workers can understand and;
- Create products or services people value.
Alright… so there is a bit more to it. It’s safe to say that most successful organisations do quality well and do it intuitively, regardless of the formality around management system certifications or their knowledge of ISO9001. However, implementing an ISO 9001 Quality Management Certification allows a business to take a systematic approach to realise and manage all the interrelated processes within the organisation. Additionally the framework also encourages businesses to strive for continual improvement and embrace a factual approach to their decision making.
Want to talk to someone about ISO 9001 Certification? Fill out this form and one of our team members will be in touch shortly
ISO 9001 Certification Overview
What is ISO 9001 Certification?
The effective implementation of an ISO 9001 certification provides a structured approach for key processes needed to deliver your product or services. Most businesses have their processes for supplying their product or services well defined and operating reasonably well. However, there is always room for improvement, and that’s where ISO 9001 comes in. Starting with a Quality Policy, the ISO9001 structure guides a suite of business processes proven to achieve quality outcomes.
The business processes covered by ISO 9001 are not solely focused on those that make your product or deliver your service. They also cover peripheral but crucial processes such as internal and external communications, responding when things go wrong, setting up measures to track performance, and recording information to identify and address potential problems. Additionally, ISO 9001 formalises the review of processes by senior management, ensuring continuous improvement and accountability.
A Quality Management System is essentially a specialised communication tool. It ensures your business understands customer needs, informs workers of their roles and responsibilities, facilitates internal communication, and provides management with measurable indicators to assess performance. ISO 9001, an internationally recognised standard, has evolved to focus on defining the processes needed to ensure product and service quality. Effective implementation of ISO 9001 has proven beneficial for a wide variety of companies worldwide.
Why do I Need ISO 9001 Certification?
ISO 9001 Quality Certification is becoming a crucial tool for the growth of many businesses around Australia. Numerous tenders, government contracts, and supplier arrangements require ISO 9001, either as a mandatory condition or as a factor in the decision-making process. This certification can differentiate you from competitors, open up new markets, or help you retain existing clients. While the certification process, including audits, might seem daunting, it is a means to an end—a necessary step to meet specific requirements.
Additionally, ISO 9001 certification provides reassurance to stakeholders that your business is sustainable and well-managed. Investors, partners, clients, workers, interest groups, and industry bodies can trust your processes, systems, and management commitments due to the transparency of the certification process. The certification indicates that your business has been independently assessed and meets or exceeds the international standard for quality management systems. Moreover, the certification process helps you manage risk and identify opportunities for improvement. It provides an independent view of your processes and systems, helping to pinpoint gaps, inconsistencies, or issues that need fixing, ultimately enhancing your business operations.
Benefits of ISO 9001 Certification
So what are the benefits of ISO 9001 certification? Usually companies initially seek certification for external reasons such as securing a preferred supplier, improving company image, or responding to customer demands. Regardless of your reasons the obvious benefit is more work. However, businesses have found that other benefits accrue from a well-implemented quality management system including better management control, a structured foundation for improving operations, more meaningful customer relations, improved business knowledge, and enhanced organisational strategy and culture.
The most tangible benefits are increased profits resulting from reduced costs due to more efficient processes, fewer defects, fewer product returns or rework, and new work from meeting tender, statutory and regulatory requirements. Other less tangible benefits include consistency of product through well-defined and documented procedures, integrated measurement of quality, efficient response to defects and learning from issues, proactive assessment of quality with processes to catch issues early, and documented procedures to help new employees understand their roles and responsibilities. Additionally, employees better understand the business’s goals and their own expected contributions, while management can better understand quality performance and react to changing circumstances. Certification also differentiates the business and demonstrates a commitment to quality deliverables.
The successful realisation of all these benefits from a quality management system heavily relies on the reason it was initiated. If the goal was merely to obtain the certification, reaping all the benefits will be more challenging. However, if there was a genuine desire to improve productivity and quality, and management are fully commitment to the ongoing support for the quality management system, then the benefits will follow.
ISO 9001 Key Principals
6 Key Principals for ISO 9001 certification:
- Customer Focus – understand what your clients want, engage with your customers and verify you are delivering what they wanted.
- Management Focus and Leadership – unity of direction, purpose and focus. Creating an environment to achieve.
- Worker engagement – a system for all people at all levels in the organisation.
- Systematic Approach – realise and manage all the interrelated processes that go into your organisation.
- Continual Improvement – strive to do things better.
- Measurement & Analysis – factual approach to decision making.
6 Step guide to ISO Quality Management Systems
Our auditors have written a 6-step guide which details the certification process which you ca expect when seeking ISO 9001 certification.
(a) Internal Requirements
Internal requirements include the organisational structure, responsibilities, relationships with clients and suppliers, existing policies, procedures and other management systems that may already be in place such as a safety or environmental management system. It also includes defining a scope for the system. The scope defines what is included and potentially excluded from the governance of the system. Will the scope include all processes at all sites and all subsidiary companies or are there valid reasons to exclude some things from the system.
(b) External Requirements
External requirements obviously includes the Quality Management Standard ISO 9001, but includes other regulatory and legislative requirements, industry requirements or other voluntary guidelines that you may subscribe to and requirements set down by your clients or government.
(a) Engage people
The system can’t be implemented effectively in isolation from key people that will be need to be involved in the system. Help people understand what will be required of them and what impacts the system will have on the way they do things moving forward. Take their feedback on board and incorporate it into the system. This is a change management project and bringing people along with you is a key to success.
(b) Leadership
Utilise top management to help influence outcomes and set objectives. They have committed to the process so get them actively involved. You will also need a Project Manager / Consultant / Management Representative a single person responsible for seeing the project through to completion – it’s not to say they may not have other duties as well and if you are reading this it’s likely the person may be you!
(c) Fit for purpose
The system needs to be fit for purpose for your organisation. Even if you start with a readymade template or a software application, you need to adapt this so that it is specific to your business. You will not be able to achieve excellence with a generic system. Representative a single person responsible for seeing the project through to completion – it’s not to say they may not have other duties as well and if you are reading this it’s likely the person may be you!
(d) Monitor
Check your progress along the way, set milestones and monitor completion of them. Don’t wait until you think your system is bullet proof and gold plated before you have it assessed. You will need to conduct internal audits so think about when these should be done and what aspects of the system are audited. Bring in your external auditors when you think you are 50-70% there and have them provide input as to where your system has gaps or non-conformances with the standard or other requirements.
(a) Stage 1 Audit
Our philosophy is that it is often more useful to have the auditor start engaging with your system when you believe you have 50-70% of the system in place. This is often the best time to conduct the stage 1 audit or a preliminary gap audit. The audit generally focuses on Head Office and the key system aspects including reviewing your documentation (such as your Quality Manual, Quality Policy and other procedures) against the mandatory requirements of ISO 9001 Quality Standard. Findings such as non-conformances, areas of concern and opportunities for improvement will provide valuable input into the development and implementation of the system. All findings will be communicated to you through a closing meeting and the audit report.
(b) Stage 2 Audit
This audit is where the magic happens. This is the certification audit and the outcome is a recommendation by the Lead Auditor to Compass Assurance Services on whether ISO 9001 certification should be granted or whether there is still some work required. This audit may be a day after the Stage 1 audit or up to 6 months after the Stage 1 audit, however most stage 2 audits occur 4-6 weeks after the initial audit. The duration between audits is really based upon the time required for you to adequately deal with any gaps or non-conformances identified at the first audit and the ability to schedule your required stakeholder to be available. Unlike the stage 1 audit implementation of the system is a key aspect of this audit. Our auditor will need to gather evidence of the system being used and implemented. This will involve engaging with workers at your various locations and in various roles associated with the system and the product realisation process.
Your certification is valid for 3 years, however this doesn’t mean that we won’t be seeing you for 3 years! Your auditor will have already worked with you on a 3 year plan which will specify the frequency of surveillance audits (typically annually or every 6 months) that will be required in order for your certification to remain valid. Surveillance audits include a sample of key processes and sites to ensure the system remains compliant with ISO 9001 and that certification of the system remains appropriate.
ISO 9001 Checklist
Our ISO 9001 auditors have developed a checklist to help you build your quality management system
Come along to one of our Workshops 9001 Quality Essentials
Gaining ISO 9001 certification / accreditation doesn’t have to be a difficult or confusing process. We’ve developed our range of essentials training courses to de-mysitify the requirements and provide a contextualised understanding of ISO 9001 to your business.
Our experienced trainers are our auditors too and focus on the areas of the standard they see business’s have difficultly with.
ISO Certification Throughout Australia
Compass Assurance Services has offices and staff located throughout Australia to assist you in achieving ISO certification. Office locations include Brisbane, Melbourne, Perth, Sydney, and Adelaide. Additionally, our auditors travel to all corners of the country, so no matter how remote your business is, our auditors will come to you.
Want to speak to someone?
Contact Us
Contact us and speak to one of our helpful team about your ISO certification needs. We can offer certification to smaller, niche standards and to other non-accredited (non ISO) standards as well.
Request a Quote
Request an obligation free quote today, tailored specifically to your business’ certification needs and industry.
Related Articles
Our 6 Steps Guide to Quality Systems and ISO 9001 Certification
1. Commitment Securing the support and commitment from top management is fundamental for the successful implementation of your Quality Management System (QMS) and attainment of ISO 9001 certification. Top management plays a pivotal role in actively participating in crucial processes such as management review and demonstrating their commitment to the…
ISO 9001 Financial Benefits
ISO 9001 Financial Benefits: Quality Management System (QMS) is one of the world’s most widely implemented standards. So, why do so many organisations invest in a QMS? And what are the financial benefits that make this a worthwhile investment….